Table of contents
Double row full complement cylindrical roller bearings
- Bearing design
- Load carrying capacity
- Compensation of angular misalignments
- Lubrication
- Sealing
- Speeds
- Noise
- Temperature range
- Cages
- Internal clearance
- Dimensions, tolerances
- Suffixes
- Structure of bearing designation
- Dimensioning
- Minimum load
- Design of bearing arrangements
- Mounting and dismounting
- Legal notice regarding data freshness
- Further information
Cylindrical roller bearings
Double row full complement cylindrical roller bearings
Double row full complement cylindrical roller bearings are suitable where:
- Bearing arrangements are subjected to particularly high radial loads ➤ section
- Not only particularly high radial forces but also axial loads from one or both directions must be supported by the bearing position (semi-locating or locating bearing function)➤ section
- Bearing arrangements must have very high rigidity
- Axial displacements of the shaft relative to the housing must be compensated without constraint in the bearing (in the case of bearings with a non-locating or semi-locating bearing function) ➤ section
- Very high radial loads occur at lower speeds, i. e., the bearings do not need to achieve speeds as high as those of cylindrical roller bearings with cage ➤ section and ➤ link
- Space-saving designs are required despite very high load
- The bearings should be separable for easier mounting (bearings with non-locating bearing function) ➤ section and ➤ section
Cylindrical roller bearing with cage/single row full complement bearing, double row full complement bearing, comparison of speed and load carrying capacity Cr = basic dynamic load rating nG = limiting speed |
![]() |
Bearing design
Design variants
The standard range of double row full complement cylindrical roller bearings comprises:
- series SL0248 and SL0249 (non-locating bearings) ➤ Figure
- series SL1850 (semi-locating bearings) ➤ Figure
- series SL0148 and SL0149 (locating bearings) ➤ Figure
- series SL0450 and SL04 (cylindrical roller bearings with annular slots – rope sheave bearings) ➤ Figure
- X-life bearings ➤ link
In addition to the bearings described here, Schaeffler supplies double row full complement cylindrical roller bearings in other types, series and dimensions. These products are described in some cases in special publications. If necessary, please contact Schaeffler. Larger catalogue bearings GL 1.
Bearings of basic design – standard range
Key features
Double row full complement cylindrical roller bearings are part of the group of radial roller bearings. These bearings comprise solid outer rings, inner rings and full complement rolling element sets. Due to the absence of a cage, the bearing can accommodate the largest possible number of rolling elements. The rollers have profiled ends, i. e. they have a slight lateral curvature towards the ends. This modified line contact between the raceways and rolling elements prevents damaging edge stresses ➤ Figure. Bearings in the standard range differ essentially in the arrangement of the ribs on the inner ring and outer ring. Depending on the design, they are used as non-locating bearings, semi‑locating bearings or locating bearings.
Series SL0248, SL0249
Bearings with non-locating bearing function
In bearings of these series, the inner ring has three rigid ribs, while the outer ring is without ribs ➤ Figure.
As a result, axial displacements of the shaft relative to the housing can be compensated within certain limits. During rotational motion, length compensation occurs without constraint in the bearing between the rollers and the raceway without ribs and is therefore practically free from friction. The maximum axial displacement s is given in the product tables. The bearings are used as non-locating bearings, i. e. they cannot guide the shaft axially in either direction ➤ section. The series SL0248 and SL0249 are not self-retaining (the outer ring without ribs can be removed from the bearing). As a result, the bearing parts (the inner ring with the rolling element set and the outer ring) can be mounted separately from each other. This gives easier mounting of the bearings ➤ section.
According to DIN 5412-9:1982, which has now been withdrawn, the bearings have the following designation:
- SL0248: NNCL48..V
- SL0249: NNCL49..V
The bearings are held together in handling and mounting by a transport and mounting retaining device on the outer ring ➤ Figure. This retaining device remains in the bearing even after mounting and must not be subjected to axial load.
Double row full complement cylindrical roller bearing – Fr = radial load
|
![]() |
Series SL1850
Bearings with semi-locating bearing function
Bearings of series SL1850 (dimension series 50) have three rigid ribs on the inner ring and one rigid rib on the outer ring ➤ Figure. In these cylindrical roller bearings, axial displacements of the shaft relative to the housing are possible in one direction only. The maximum axial displacement s is given in the product tables ➤ link. The bearings are used as semi-locating bearings, i. e. they can guide the shaft axially in one direction ➤ section.
The bearings are held together in handling and mounting by a transport and mounting retaining device on the outer ring ➤ Figure.
This retaining device remains in the bearing even after mounting and must not be subjected to axial load.
Double row full complement cylindrical roller bearing – Fr = radial load Fa = axial load
|
![]() |
Series SL0148, SL0149
Bearings with locating bearing function
In these bearings, the inner ring has three rigid ribs and the outer ring has two rigid ribs ➤ Figure. Axial displacements between the shaft and housing are not possible. The bearings are used as locating bearings, i. e. they can guide the shaft axially in both directions ➤ section.
According to DIN 5412-9:1982, which has now been withdrawn, the bearings have the following designation:
- SL0148: NNC48..V
- SL0149: NNC49..V
The split outer ring is held together by a transport and mounting retaining device ➤ Figure. This retaining device remains in the bearing even after mounting and must not be subjected to axial load.
Double row full complement cylindrical roller bearing – Fr = radial load Fa = axial load
|
![]() |
Series SL0450..-PP and SL04..-PP – cylindrical roller bearings with annular slots
Bearings with locating bearing function, particularly suitable for the support of rope sheaves
These bearings comprise solid outer rings without ribs, inner rings with three ribs, rib-guided rolling element sets and sealing rings ➤ Figure. The outer rings have annular slots for retaining rings. The inner rings are axially split, 1 mm wider than the outer rings and held together by a sheet metal ring. They are used as locating bearings (but can support only slight axial loads) and are used in preference for the support of rope sheaves.
Light series and dimension series 50
Cylindrical roller bearings with annular slots are available as a light series SL04..-PP and in the dimension series 50 as SL0450..-PP. The latter has a higher load carrying capacity than the light series ➤ link.
Extensive information on rope sheave bearing arrangements is given in the Technical Product Information TPI 237. This publication can be requested from Schaeffler.
Double row full complement cylindrical roller bearing with annular slots – Fr = radial load Fa = axial load
|
![]() |
X-life premium quality
Double row full complement cylindrical roller bearings of series SL1850 are available in many sizes as X-life bearings ➤ link. These bearings exhibit considerably higher performance than comparable standard cylindrical roller bearings. This is achieved, for example, through the modified internal construction, the optimised contact geometry between the rollers and raceways, the better surface quality and the optimised roller guidance and lubricant film formation.
Advantages
Increased customer benefits due to X-life
These technical enhancements offer a range of advantages, such as:
- a more favourable load distribution in the bearing and thus a higher dynamic load carrying capacity of the bearings
- a higher fatigue limit load
- lower heat generation in the bearing
- lower lubricant consumption and therefore longer maintenance intervals if relubrication is carried out
- a measurably longer operating life of the bearings
- high operational security
- compact, environmentally-friendly bearing arrangements
Interchangeable with comparable standard bearings
Since X-life cylindrical roller bearings have the same dimensions as the corresponding standard bearings, the latter can be replaced without any problems by the higher-performance X-life bearings. The major advantages of X-life can therefore also be used for existing bearing arrangements with standard bearings.
Lower operating costs, higher machine availability
In conclusion, these advantages improve the overall cost-efficiency of the bearing position significantly and thus bring about a sustainable increase in the efficiency of the machine and equipment.
Suffix XL
X-life cylindrical roller bearings include the suffix XL in the designation ➤ section and ➤ link.
Areas of application
Due to their special technical features, double row full complement X-life cylindrical roller bearings are highly suitable, for example, for bearing arrangements in:
- heavy industry (steel production)
- power transmission (gearbox engineering)
- processing machines and construction machinery
- wind turbines (gearbox applications)
X-life indicates a high product performance density and thus a particularly significant benefit to the customer. Further information on X-life ➤ link.
Load carrying capacity
Designed for very high radial loads
Depending on the type, double row full complement cylindrical roller bearings can support not only very high radial forces but also high axial loads on one or both sides:
- The series SL0248 and SL0249 must not be subjected to radial load
- The series SL1850 can support radial loads as well as axial loads on one side
- The series SL0148 and SL0149 can support radial loads as well as axial loads on both sides
- The series SL0450..-PP and SL04..50-PP can support radial loads and are suitable for the support of moderate axial loads from both directions
Higher axial load carrying capacity of bearings with toroidal crowned roller end face
Neither wear nor material fatigue occurs on the rib contact running and roller end faces
In the case of cylindrical roller bearings with toroidal crowned rollers (TB design), the axial load carrying capacity has been significantly improved with the aid of new calculation and manufacturing methods. A special curvature of the roller end faces facilitates optimum contact conditions between the rollers and ribs ➤ Figure. As a result, the axial contact pressures on the rib are significantly minimised and a lubricant film capable of supporting higher loads is formed. Under standard operating conditions, this completely eliminates wear and fatigue at the rib contact running and roller end faces. In addition, the axial frictional torque is reduced by up to 50%. The bearing temperature during operation is therefore significantly lower. Bearings of toroidal crowned design ➤ link.
By agreement, bearings of series SL1850 are available starting from a bore diameter d = 180 mm in the TB design.
Contact geometry of roller end face/rib face – modified roller end faces
|
![]() |
Load ratio Fa/Fr
Ratio Fa/Fr ≦ 0,4 or 0,6
The bearings can support axial loads on one side by means of the ribs on the inner and outer ring ➤ Figure. In order to ensure problem-free running (tilting of the rollers is prevented), they must always be subjected to radial load at the same time as axial load. The ratio Fa/Fr must not exceed the value 0,4. For bearings with toroidal roller ends (TB design), values up to 0,6 are permissible.
Continuous axial loading without simultaneous radial loading is not permissible.
Permissible axial load
Influencing factors on the axial load carrying capacity
Axial loads are supported by the bearing ribs and the roller end faces ➤ Figure. The axial load carrying capacity of the bearing is therefore essentially dependent on:
- the size of the sliding surfaces between the ribs and the end faces of the rolling elements
- the sliding velocity at the ribs
- the lubrication of the contact surfaces
- tilting of the bearing
- friction
Force flow under axial load – semi‑locating bearing SL1850 |
![]() |
Calculation of permissible axial load – cylindrical rollers with conventional roller ends
Bearings with standard roller ends
The permissible axial load Fa per can be calculated from the hydrodynamic load carrying capacity of the contact ➤ Equation.
Permissible axial load – bearings of standard design

Legend
Fa per | N |
Permissible continuous axial load. In order to prevent unacceptably high temperatures in the bearing, Fa per must not be exceeded |
Fa max | N |
Maximum continuous axial load in relation to rib fracture. In order to prevent unacceptably high pressures at the contact surfaces, Fa max must not be exceeded |
kS | - |
Factor as a function of lubrication method ➤ Table. The factor takes into consideration the lubrication method used for the bearing. The better the lubrication and in particular the heat dissipation, the higher the permissible axial load |
kB | - |
Factor as a function of bearing series ➤ Table |
dM | mm |
Mean bearing diameter dM = (D + d)/2 ➤ link |
n | min-1 |
Operating speed |
Factor kS
Lubrication method |
Factor kS |
|
---|---|---|
from |
up to |
|
Standard greasing, no heat dissipation by the lubricant |
1,5 |
3 |
Minimal heat dissipation, drip feed oil lubrication, |
7,5 |
10 |
Poor heat dissipation, oil sump lubrication, |
10 |
15 |
Good heat dissipation, recirculating oil lubrication |
12 |
18 |
Very good heat dissipation, recirculating oil lubrication |
16 |
24 |
The precondition for these kS values is an operating viscosity of the lubricant of at least the reference viscosity ν1 in accordance with DIN ISO 281:2010.
Doped lubricating oils should be used, such as CLP (DIN 51517) and HLP (DIN 51524) of ISO-VG-grades 32 to 460 and ATF oils (DIN 51502) and transmission oils (DIN 51512) of SAE viscosity grades 75W to 140W.
Bearing factor kB
Series |
kB |
---|---|
SL0148 |
4,5 |
SL0149 |
11 |
SL1850 |
17 |
SL0450 |
17 |
SL04 |
10 |
Calculation of permissible axial load – cylindrical rollers with toroidal crowned roller ends
For bearings with toroidal roller ends, the permissible axial loads are 50% higher ➤ Equation.
Permissible axial load – bearings of TB design

Calculation of maximum permissible axial load
For bearings with rollers of the standard or TB design, the maximum permissible axial load Fa max ➤ Equation is calculated from the rib strength and the security against wear. This must not be exceeded, even if Fa per gives higher values ➤ Equation.
Maximum axial load – bearings of standard and TB design

Permissible axial load
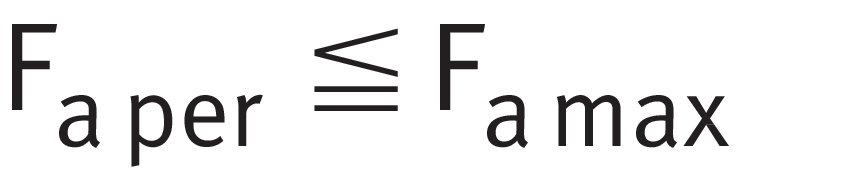
Axial load carrying capacity of cylindrical roller bearings with annular slots (rope sheave bearings)
For cylindrical roller bearings with annular slots in the outer ring, the calculations of Fa per and Fa max cannot be used. For the axial load carrying capacity of these bearings, please consult Schaeffler.
Compensation of angular misalignments
The bearings do not permit any misalignments between the inner and outer ring, i. e. the bearing positions must be well aligned.
Lubrication
Oil or grease lubrication is possible
The cylindrical roller bearings are not greased. They must be lubricated with oil or grease. The bearings can be lubricated via the end faces of the outer ring as well as via a lubrication groove and lubrication holes in the outer ring.
Cylindrical roller bearings with annular slots (rope sheave bearings)
The bearings have an initial greasing
These bearings are supplied greased and can be relubricated via the outer ring or inner ring. The grease used is a lithium complex soap grease to GA08. Arcanol LOAD150 ➤ link is suitable for relubrication. The greases named are highly suitable, due to their good moisture resistance and high load carrying capacity, for applications in rope sheaves at low to moderate speeds.
If there is any uncertainty regarding the suitability of the selected lubricant for the application, please consult Schaeffler or the lubricant manufacturer.
Sealing
Providing additional seals in the adjacent construction
The bearings are not sealed; i. e. sealing of the bearing position must be carried out in the adjacent construction. This must reliably prevent:
- moisture and contaminants from entering the bearing
- the egress of lubricant from the bearing
Cylindrical roller bearings with annular slots (rope sheave bearings)
The bearings are sealed on both sides
In the case of these bearings, the rolling element system is protected against contamination and moisture by polyurethane sealing rings on both sides. The seals have low friction and are particularly resistant to climate and temperature. Where environmental conditions are particularly critical, sealing of the bearings can be improved further by means of additional seals, such as V rings, in the adjacent construction.
Speeds
Limiting speeds and reference speeds in the product tables
The product tables give two speeds for most bearings:
- the kinematic limiting speed nG
- the thermal speed rating nϑ
Lower speed capacity than bearings with cage
Due to the kinematic conditions, full complement cylindrical roller bearings do not achieve the high speeds that are possible when using cylindrical roller bearings with cage.
Limiting speeds
The limiting speed nG is the kinematically permissible speed of the bearing. Even under favourable mounting and operating conditions, this value should not be exceeded without prior consultation with Schaeffler ➤ link.
Reference speeds
nϑr is used to calculate nϑ
The thermal speed rating nϑr is not an application-oriented speed limit, but is a calculated ancillary value for determining the thermally safe operating speed nϑ ➤ link.
Bearings with contact seals
For bearings with contact seals, no speed ratings are defined in accordance with DIN ISO 15312:2004. As a result, only the limiting speed nG is given in the product tables for these bearings.
Noise
The Schaeffler Noise Index (SGI) has been developed as a new feature for comparing the noise level of different bearing types and series. As a result, a noise evaluation of rolling bearings can now be carried out for the first time.
Schaeffler Noise Index
The SGI value is based on the maximum permissible noise level of a bearing in accordance with internal standards, which is calculated on the basis of ISO 15242. In order that different bearing types and series can be compared, the SGI value is plotted against the basic static load rating C0.
This permits direct comparisons between bearings with the same load carrying capacity. The upper limit value is given in each of the diagrams. This means that the average noise level of the bearings is lower than illustrated in the diagram.
The Schaeffler Noise Index is an additional performance characteristic in the selection of bearings for noise-sensitive applications. The specific suitability of a bearing for an application in terms of installation space, load carrying capacity or speed limit for example, must be checked independently of this.
Schaeffler Noise Index SGI = Schaeffler Noise Index C0 = basic static load rating |
![]() |
Temperature range
Limiting values
The operating temperature of the bearings is limited by:
- the dimensional stability of the bearing rings and cylindrical rollers
- the lubricant
- the seals
Possible operating temperatures of double row cylindrical roller bearings ➤ Table.
Permissible temperature ranges
Operating temperature |
Open full complement bearings |
Rope sheave bearings |
---|---|---|
|
–30 °C to +120 °C |
–20 °C to +80 °C, –40 °C to +80 °C |
In the event of anticipated temperatures which lie outside the stated values, please contact Schaeffler.
Cages
Full complement cylindrical roller bearings do not have a cage for guidance and separation of the rolling elements. The cylindrical rollers are guided by the ribs on the bearing rings.
Internal clearance
Radial internal clearance
The standard is CN
Double row full complement cylindrical roller bearings are manufactured as standard with the radial internal clearance CN (normal) ➤ Table. CN is not stated in the designation.
Certain sizes are also available by agreement with the larger internal clearance C3, C4 and C5 ➤ Table.
The values for radial internal clearance correspond to DIN 620-4:2004 (ISO 5753-1:2009) ➤ Table. They are valid for bearings which are free from load and measurement forces (without elastic deformation).
Radial internal clearance of double row full complement cylindrical roller bearings
Nominal |
Radial internal clearance |
||||||||
---|---|---|---|---|---|---|---|---|---|
d |
CN (Group N) |
C3 (Group 3) |
C4 (Group 4) |
C5 (Group 5) |
|||||
mm |
μm |
μm |
μm |
μm |
|||||
over |
incl. |
min. |
max. |
min. |
max. |
min. |
max. |
min. |
max. |
‒ |
24 |
20 |
45 |
35 |
60 |
50 |
75 |
65 |
90 |
24 |
30 |
20 |
45 |
35 |
60 |
50 |
75 |
70 |
95 |
30 |
40 |
25 |
50 |
45 |
70 |
60 |
85 |
80 |
105 |
40 |
50 |
30 |
60 |
50 |
80 |
70 |
100 |
95 |
125 |
50 |
65 |
40 |
70 |
60 |
90 |
80 |
110 |
110 |
140 |
65 |
80 |
40 |
75 |
65 |
100 |
90 |
125 |
130 |
165 |
80 |
100 |
50 |
85 |
75 |
110 |
105 |
140 |
155 |
190 |
100 |
120 |
50 |
90 |
85 |
125 |
125 |
165 |
180 |
220 |
120 |
140 |
60 |
105 |
100 |
145 |
145 |
190 |
200 |
245 |
140 |
160 |
70 |
120 |
115 |
165 |
165 |
215 |
225 |
275 |
160 |
180 |
75 |
125 |
120 |
170 |
170 |
220 |
250 |
300 |
180 |
200 |
90 |
145 |
140 |
195 |
195 |
250 |
275 |
330 |
200 |
225 |
105 |
165 |
160 |
220 |
220 |
280 |
305 |
365 |
225 |
250 |
110 |
175 |
170 |
235 |
235 |
300 |
330 |
395 |
250 |
280 |
125 |
195 |
190 |
260 |
260 |
330 |
370 |
440 |
280 |
315 |
130 |
205 |
200 |
275 |
275 |
350 |
410 |
485 |
315 |
355 |
145 |
225 |
225 |
305 |
305 |
385 |
455 |
535 |
355 |
400 |
190 |
280 |
280 |
370 |
370 |
460 |
510 |
600 |
Radial load carrying capacity of cylindrical roller bearings with annular slots (rope sheave bearings)
The correct radial internal clearance is of decisive importance for the correct function of rope sheaves. The radial internal clearance group is dependent on the material of the rope sheave ➤ Table.
Radial internal clearance of cylindrical roller bearings with annular slots for the support of rope sheaves as a function of the material of adjacent parts – recommendation
Nominal |
Material of rope sheave |
||
---|---|---|---|
d |
Steel |
Plastic |
|
mm |
Internal clearance group of bearing |
||
over |
incl. |
||
‒ |
85 |
CN or C3 |
C5 |
85 |
300 |
C3 |
C5 |
Dimensions, tolerances
Dimension standards
The main dimensions of cylindrical roller bearings correspond to ISO 15:2017 (DIN 616:2000).
Chamfer dimensions
The limiting dimensions for chamfer dimensions correspond to DIN 620-6:2004.
Tolerances
The dimensional and running tolerances of the cylindrical roller bearings correspond to the tolerance class Normal in accordance with ISO 492:2014. Tolerance values in accordance with ISO 492 ➤ link.
Suffixes
For a description of the suffixes used in this chapter ➤ Table, cylindrical roller bearings with annular slots ➤ Table and medias interchange http://www.schaeffler.de/std/1B69.
Suffixes and corresponding descriptions, double row full complement cylindrical roller bearings
Suffix |
Description of suffix |
|
---|---|---|
BR |
Black oxide coated |
Available by agreement |
C3 |
Radial internal clearance C3 (larger than normal) |
Available by agreement |
C4 |
Radial internal clearance C4 (larger than C3) |
Available by agreement |
C5 |
Radial internal clearance C5 (larger than C4) |
Available by agreement |
TB |
Bearing with increased axial load carrying capacity |
Standard, dependent on bore code and bearing series |
XL |
X-life bearing |
Standard, dependent on bore code and bearing series |
Suffixes and corresponding descriptions, cylindrical roller bearings with annular slots (rope sheave bearings)
Suffix |
Description of suffix |
|
---|---|---|
C3 |
Radial internal clearance C3 (larger than normal) |
Special design, available by agreement |
C4 |
Radial internal clearance C4 (larger than C3) |
Special design, available by agreement |
C5 |
Radial internal clearance C5 (larger than C4) |
Special design, available by agreement |
D |
Improved outer ring profile, with an enlarged load-bearing area and optimised edge transitions |
Standard |
GA22 |
Bearing greased with lithium soap grease GA22 for expanded temperature range |
Special design, available by agreement |
P |
Contact seal on one side |
Special design, available by agreement |
PP |
Contact seal on both sides |
Standard |
RR |
Corrosion-resistant design, with Corrotect coating |
Special design, available by agreement |
2NR |
Supplied with two loose-packed retaining rings WRE |
Special design, available by agreement |
2WR |
Supplied with two loose-packed retaining rings WR |
Special design, available by agreement |
‒ |
Without seals |
Special design, available by agreement |
Structure of bearing designation
Examples of composition of bearing designation
The designation of bearings follows a set model. Examples are shown in ➤ Figure and ➤ Figure. The composition of designations is subject to DIN 623-1 ➤ Figure.
Double row full complement cylindrical roller bearing (semi‑locating bearing): designation structure |
![]() |
Double row full complement cylindrical roller bearing (rope sheave bearing): designation structure |
![]() |
Dimensioning
Equivalent dynamic bearing load
P = Fr under purely radial load of constant magnitude and direction
The basic rating life equation L = (Cr/P)p used in the dimensioning of bearings under dynamic load assumes a load of constant magnitude and direction. In radial bearings, this is a purely radial load Fr. If this condition is met, the bearing load Fr is used in the rating life equation for P (P = Fr).
Bearings with non-locating bearing function and cylindrical roller bearings with annular slots (rope sheave bearings)
P = Fr
Non-locating bearings can only support radial loads, rope sheave bearings only have a small axial load carrying capacity. For these bearings ➤ Equation.
Equivalent dynamic load
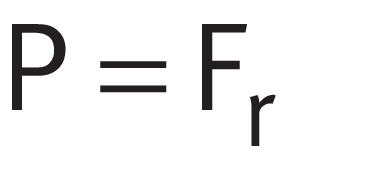
Cylindrical roller bearings with semi-locating and locating bearing function
P is a substitute force for combined load and various load cases
If the condition described above is not met, i. e. if in addition to the radial force Fr, there is also an axial force Fa, a constant radial force must first be determined for the rating life calculation that (in relation to the rating life) represents an equivalent load. This force is known as the equivalent dynamic bearing load P.
Fa/Fr ≦ e or Fa/Fr > e
The calculation of P is dependent on the load ratio Fa/Fr and the calculation factors e and Y ➤ Equation and ➤ Equation.
Equivalent dynamic load
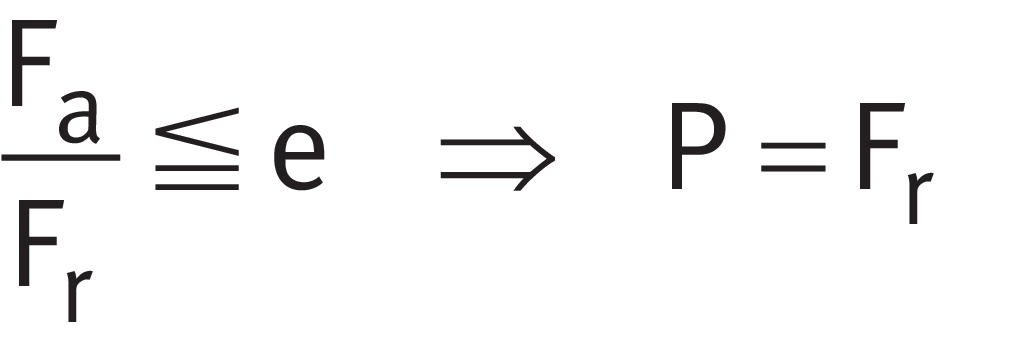
Equivalent dynamic load

Legend
P | N |
Equivalent dynamic bearing load |
Fr | N |
Radial load |
Fa | N |
Axial load |
e, Y | - |
Factors ➤ Table |
Factors e and Y
Bearing series |
Calculation factors |
|
---|---|---|
e |
Y |
|
SL1850 |
0,2 |
0,6 |
SL0148, SL0149 |
0,24 |
0,5 |
Equivalent static bearing load
P0 ≧ F0r
For cylindrical roller bearings subjected to static load ➤ Equation.
Equivalent static load
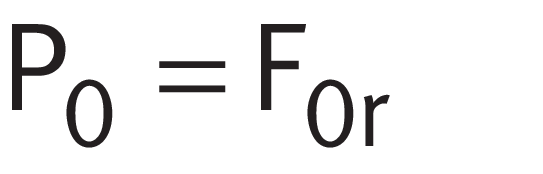
Legend
P0 | N |
Equivalent static bearing load |
F0r | N |
Largest radial load present (maximum load) |
Static load safety factor
S0 = C0/P0
In addition to the basic rating life L (L10h), it is also always necessary to check the static load safety factor S0 ➤ Equation.
Static load safety factor
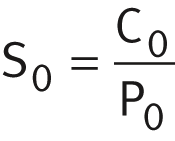
Legend
S0 | - |
Static load safety factor |
C0 | N |
Basic static load rating |
P0 | N |
Equivalent static bearing load |
Minimum load
In order to prevent slippage damage, a minimum radial load of P > C0r/60 is necessary during continuous operation
In order that no slippage occurs between the contact partners, the cylindrical roller bearings must be constantly subjected to a sufficiently high radial load. For continuous operation, experience shows that a minimum radial load of the order of P > C0r/60 is necessary. In most cases, however, the radial load is already higher than the requisite minimum load due to the weight of the supported parts and the external forces.
If the minimum radial load is lower than indicated above, please consult Schaeffler.
Design of bearing arrangements
Support bearing rings over their entire circumference and width
In order to allow full utilisation of the load carrying capacity of the bearings and thus also achieve the requisite rating life, the bearing rings must be rigidly and uniformly supported by means of contact surfaces over their entire circumference and over the entire width of the raceway. Support can be provided by means of a cylindrical seating surface. The seating and contact surfaces should not be interrupted by grooves, holes or other recesses. The accuracy of mating parts must meet specific requirements ➤ Table to ➤ Table.
Radial location
For secure radial location, tight fits are necessary
In addition to supporting the rings adequately, the bearings must also be securely located in a radial direction, to prevent creep of the bearing rings on the mating parts under load. This is generally achieved by means of tight fits between the bearing rings and the mating parts. If the rings are not secured adequately or correctly, this can cause severe damage to the bearings and adjacent machine parts. Influencing factors, such as the conditions of rotation, magnitude of the load, internal clearance, temperature conditions, design of the mating parts and the mounting and dismounting options must be taken into consideration in the selection of fits.
If shock type loads occur, tight fits (transition fit or interference fit) are required to prevent the rings from coming loose at any point. Clearance, transition or interference fits ➤ link.
The following information provided in Technical principles must be taken into consideration in the design of bearing arrangements:
- conditions of rotation ➤ link
- tolerance classes for cylindrical shaft seats (radial bearings) ➤ link
- shaft fits ➤ link
- tolerance classes for bearing seats in housings (radial bearings) ➤ link
- housing fits ➤ link
Radial location of cylindrical roller bearings with annular slots (rope sheave bearings)
The outer ring must have an interference fit to achieve rigid seating
The axial loads occurring cannot be securely transmitted by the retaining rings. Transmission of the loads is only possible if sufficient joint pressure is present. Due to the operating conditions present in rope sheave bearing arrangements, an interference fit between the outer ring and rope sheave is absolutely critical in order to achieve correct bearing function and load transmission. The joint pressure must be between pmin = 2 N/mm2 and pmax = 25 N/mm2. The internal clearance has a considerable influence on bearing function ➤ Table.
Axial location
The bearings must also be securely located in an axial direction
As a tight fit alone is not normally sufficient to also locate the bearing rings securely on the shaft and in the housing bore in an axial direction, this must usually be achieved by means of an additional axial location or retention method. The axial location of the bearing rings must be matched to the type of bearing arrangement. Shaft and housing shoulders, housing covers, nuts, spacer rings, retaining rings, adapter and withdrawal sleeves etc. are generally suitable; example ➤ Figure.
Axial location of cylindrical roller bearings with annular slots (rope sheave bearings)
Axial location is carried out by means of retaining rings
The annular slots allow axial location of the outer rings using retaining rings ➤ Figure. Suitable fasteners are WRE rings or rings in accordance with DIN 471. Locating rings are not included in the scope of delivery. The design 2NR is supplied with two retaining rings WRE packed loose. The split inner ring must be axially secured ➤ Figure. The fasteners must not be subjected to axial load.
Arrangement of several rope sheaves adjacent to each other
If housing tolerances are present or several rope sheaves are arranged adjacent to each other, axial clearance may occur between the inner rings. This must always be prevented by means of design measures. For example, shims are suitable for this purpose.
Cylindrical roller bearing with annular slots (rope sheave bearing) –
|
![]() |
Dimensional, geometrical and running accuracy of cylindrical bearing seats
A minimum of IT6 should be provided for the shaft seat and a minimum of IT7 for the housing seat
The accuracy of the cylindrical bearing seat on the shaft and in the housing should correspond to the accuracy of the bearing used. For cylindrical roller bearings with the tolerance class Normal, the shaft seat should correspond to a minimum of standard tolerance grade IT6 and the housing seat to a minimum of IT7. Guide values for the geometrical and positional tolerances of the bearing seating surfaces ➤ Table, tolerances t1 to t3 in accordance with ➤ link. Numerical values for IT grades ➤ Table.
Guide values for the geometrical and positional tolerances of bearing seating surfaces
Bearing |
Bearing seating surface |
Standard tolerance grades to ISO 286-1 |
||||
---|---|---|---|---|---|---|
to ISO 492 |
to DIN 620 |
Diameter tolerance |
Roundness tolerance |
Parallelism tolerance |
Total axial runout tolerance of abutment shoulder |
|
t1 |
t2 |
t3 |
||||
Normal |
PN (P0) |
Shaft |
IT6 (IT5) |
Circumferential load IT4/2 |
Circumferential load IT4/2 |
IT4 |
Shaft | IT6 (IT5) |
Point load IT5/2 |
Point load IT5/2 |
IT4 | ||
Housing |
IT7 (IT6) |
Circumferential load IT5/2 |
Circumferential load IT5/2 |
IT5 |
||
Housing | IT7 (IT6) |
Point load IT6/2 |
Point load IT6/2 |
IT5 |
Numerical values for ISO standard tolerances (IT grades) to ISO 286-1:2010
IT grade |
Nominal dimension in mm |
||||||||
---|---|---|---|---|---|---|---|---|---|
over |
18 |
30 |
50 |
80 |
120 |
180 |
250 |
315 |
|
incl. |
30 |
50 |
80 |
120 |
180 |
250 |
315 |
400 |
|
Values in μm |
|||||||||
IT4 |
6 |
7 |
8 |
10 |
12 |
14 |
16 |
18 |
|
IT5 |
9 |
11 |
13 |
15 |
18 |
20 |
23 |
25 |
|
IT6 |
13 |
16 |
19 |
22 |
25 |
29 |
32 |
36 |
|
IT7 |
21 |
25 |
30 |
35 |
40 |
46 |
52 |
57 |
Roughness of cylindrical bearing seating surfaces
Ra must not be too high
The roughness of the bearing seats must be matched to the tolerance class of the bearings. The mean roughness value Ra must not be too high, in order to maintain the interference loss within limits. The shafts must be ground, while the bores must be precision turned. Guide values as a function of the IT grade of bearing seating surfaces ➤ Table.
Roughness values for cylindrical bearing seating surfaces – guide values
Nominal diameter d (D) |
Recommended mean roughness value Ramax |
||||
---|---|---|---|---|---|
mm |
μm |
||||
Diameter tolerance (IT grade) |
|||||
over |
incl. |
IT7 |
IT6 |
IT5 |
IT4 |
‒ |
80 |
1,6 |
0,8 |
0,4 |
0,2 |
80 |
500 |
1,6 |
1,6 |
0,8 |
0,4 |
Bearing seat design (roughness) for cylindrical roller bearings with annular slots (rope sheave bearings)
Recommended roughness values for bearing seating surfaces ➤ Table.
Roughness for bearing seating surfaces on the shaft and in the housing bore for cylindrical roller bearings with annular slots – recommendation
Nominal diameter d (D) |
Roughness |
||
---|---|---|---|
mm |
|||
over |
incl. |
Shaft |
Housing bore |
20 |
300 |
Rz 4 |
Rz 16 |
Mounting dimensions for the contact surfaces of bearing rings
The contact surfaces for the rings must be of sufficient height
The mounting dimensions of the shaft and housing shoulders, and spacer rings etc., must ensure that the contact surfaces for the bearing rings are of sufficient height. The transition from the bearing seat to the abutment shoulder must be designed with rounding to DIN 5418:1993 or an undercut to DIN 509:2006. Proven mounting dimensions for the radii and diameters of abutment shoulders are given in the product tables ➤ link. These dimensions are limiting dimensions (maximum or minimum dimensions); the actual values should not be higher or lower than specified.
Rib support in axially loaded bearings
Ribs under axial load must be supported over their entire height and entire circumference ➤ link and ➤ Figure. The size and axial runout accuracy of the contact surfaces on the inner ring rib must be observed especially in the case of cylindrical roller bearings subjected to high loads, since these factors also influence the uniformity of the rib load and the running accuracy of the shaft. This means that the ribs may be subjected to damaging alternating stresses even in the case of very small misalignments. If the mounting dimensions indicated in the product tables are observed, the problems described can be reliably avoided ➤ link.
Support in semi-locating bearings
In semi-locating bearings, it is sufficient to support the bearing rings on one side, on the rib supporting the axial load ➤ Figure.
Support of inner ring rib supporting axial load dc = recommended height of shaft shoulder with axially loaded rib Arrow = force flow |
![]() |
Support of sealing rings in cylindrical roller bearings with annular slots (rope sheave bearings)
Observe the abutment dimension of the sealing rings
The sealing rings must be supported to a sufficient height that they are not pressed out during lubrication of the bearings ➤ Figure. The dimension d2 in the product tables must be observed ➤ dimension table.
Rope sheave bearings – d2 = abutment dimension
|
![]() |
Mounting and dismounting
The mounting and dismounting options for cylindrical roller bearings, by thermal, hydraulic or mechanical methods, must be taken into consideration in the design of the bearing position.
As the bearings are not self-retaining, they are easy to mount
The series SL0248 and SL0249 are not self-retaining. As a result, the bearing parts (the inner ring with the rolling element set and the outer ring) can be mounted separately from each other ➤ section. This gives simplified mounting of the bearings, especially when the two bearing rings have a tight fit.
Mounting and dismounting of cylindrical roller bearings with annular slots (rope sheave bearings)
During mounting and dismounting of the bearings, the mounting forces must never be directed through the rolling elements, sealing rings or the fasteners on the split bearing ring.
Schaeffler Mounting Handbook
Rolling bearings must be handled with great care
Rolling bearings are well-proven precision machine elements for the design of economical and reliable bearing arrangements, which offer high operational security. In order that these products can function correctly and achieve the envisaged operating life without detrimental effect, they must be handled with care.
The Schaeffler Mounting Handbook MH 1 gives comprehensive information about the correct storage, mounting, dismounting and maintenance of rotary rolling bearings http://www.schaeffler.de/std/1B68. It also provides information which should be observed by the designer, in relation to the mounting, dismounting and maintenance of bearings, in the original design of the bearing position. This book is available from Schaeffler on request.
Legal notice regarding data freshness
The further development of products may also result in technical changes to catalogue products
Of central interest to Schaeffler is the further development and optimisation of its products and the satisfaction of its customers. In order that you, as the customer, can keep yourself optimally informed about the progress that is being made here and with regard to the current technical status of the products, we publish any product changes which differ from the printed version in our electronic product catalogue.
We therefore reserve the right to make changes to the data and illustrations in this catalogue. This catalogue reflects the status at the time of printing. More recent publications released by us (as printed or digital media) will automatically precede this catalogue if they involve the same subject. Therefore, please always use our electronic product catalogue to check whether more up-to-date information or modification notices exist for your desired product.
Further information
In addition to the data in this chapter, the following chapters in Technical principles must also be observed in the design of bearing arrangements: